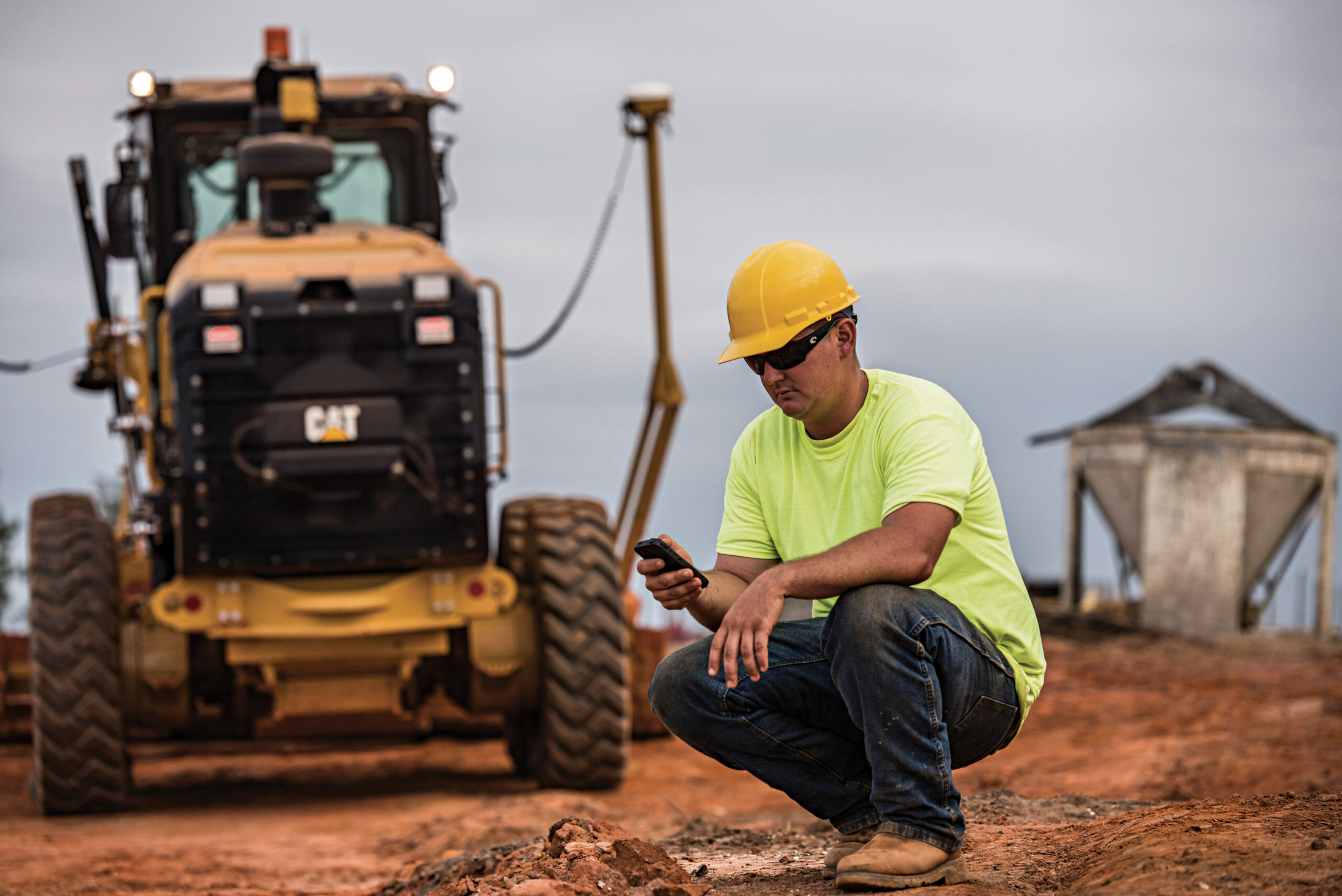
Published on November 12, 2020
Using VisionLink™ for Preventive Maintenance
We’ve all heard the old adage “an ounce of prevention is worth a pound of cure.” Nowhere is that more applicable than maintaining expensive, heavy equipment. Outside of your payroll, the purchase and maintenance of your machines are more than likely two of the larger line items in your budget.
At Ziegler, we understand the short-term and long-term value of caring for your equipment routinely. And for that reason, we’ve tried to simplify the process through a technology we refer to as VisionLink Preventive Maintenance (VLPM).
Think of Preventive Maintenance or PM the same way that you would an annual health physical. The objective is identical: identify small problems early and address them before they become big problems. In the case of heavy equipment, changing fluids and lubrication are probably two of the most common PM activities Ziegler undertakes, but of course there are others.
One of the principle challenges for most operators is keeping track of their maintenance schedule while also trying to keep projects moving forward along with all of the other administrative headaches that come with running a business. However, if PM is ignored, the consequence can be expensive in terms of money and time, both of which affect the bottom line. That’s where the technology comes in.
Through the online fleet management tool called VisionLink, you can consolidate your fleet’s maintenance programming and PM scheduling into one digital system, monitoring each machine based on its operation hours and generating reports on every machine you have logged into the system. This resource enables you to assess your PM activity whenever and wherever you need to. And with a simple user interface that will guide you through an initial, short set-up, you can organize your PM activities with confidence.
Step-By-Step instructions for how to set up PM’s in VisionLink:
1. Cat® equipment in VisionLink will come with a preset “Operations or Repair Options” of intervals and parts inventory for each machine. This setup may require no changes for many customers
2. If you wish to change parts or interval settings –Select the maintenance wrench on left side, this will display a list of assets. Select an asset, then click on the 3 dots in the upper right and select “Add/Manage Intervals”. Select the interval where changes are to be made and then select the 3 dots in the upper right again to choose “Edit”.
3. When changes are completed go to the bottom right and select “Save”.
Posted In: Technology